Whatever your activity, optimizing your inventory management is key to reducing the many associated costs, such as capital investments, risks, deterioration, insurance, personnel, logistics, and infrastructure. The ease or difficulty of accurately predicting a demand through the correct demand planning process, depends on your business activities. Some items may show a good forecast accuracy while others can demonstrate intermittent demand and are therefore difficult to predict.
Therefore, understanding the different inventory policies allows you to choose the most suitable system in relation to the cost strategy associated with each item.
An inventory system sets out "how many" parts to order or manufacture. There are three options:
- Lot for lot: in which the order exactly matches the consumption requirements for the period
- Fixed order quantity: for example, this might depend on the packaging (or multiples of these lots)
- n periods of supply: a quantity large enough to meet demands during these n periods.
An inventory policy also specifies "when" to place purchase orders or manufacturing orders. Two options are referenced:
- Order point: the order is triggered when the stock falls below a certain threshold (for example, an order is made when there are fewer than 10 items available in stock).
- Periodic replenishment: The time between two orders is fixed (for example, an order is placed every Monday morning).
In this article we will cover two commonly used policies:
- The order point (fixed replenishment)
- Periodic replenishment (variable quantity)

Try our fast & simple demand forecasting solution
Sign up for free to SKU Science today!
Pre-loaded sample data - No credit card required
Order point policy (fixed replenishment)
This method is used when an order of the same quantity is placed with a supplier (or a production order) every time the level of available stock falls below a predetermined threshold. See example below: If 3, or fewer than 3, items remain in stock, a replenishment order is generated and will always be fixed at 10 items.
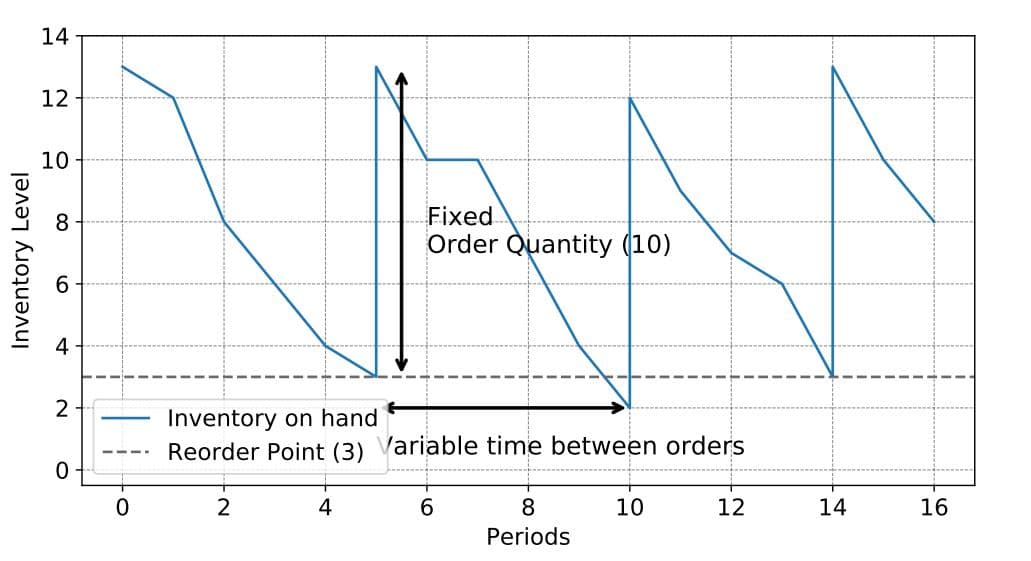
Benefits: This is a reassuring policy that allows you to place an order whenever necessary.
Limitations: It does not allow you to group orders with the same supplier, which can incur additional costs.
Periodic replenishment (of variable quantity)
This is a “fixed schedule” replenishment system, where the time between two replenishment orders is the same.
The quantity ordered during each period is always different, and is based on the stock target and the inventory position at the time of the order.
In the example below, we show an order placed every 5 periods, so as to reach a final stock level equal to 13.
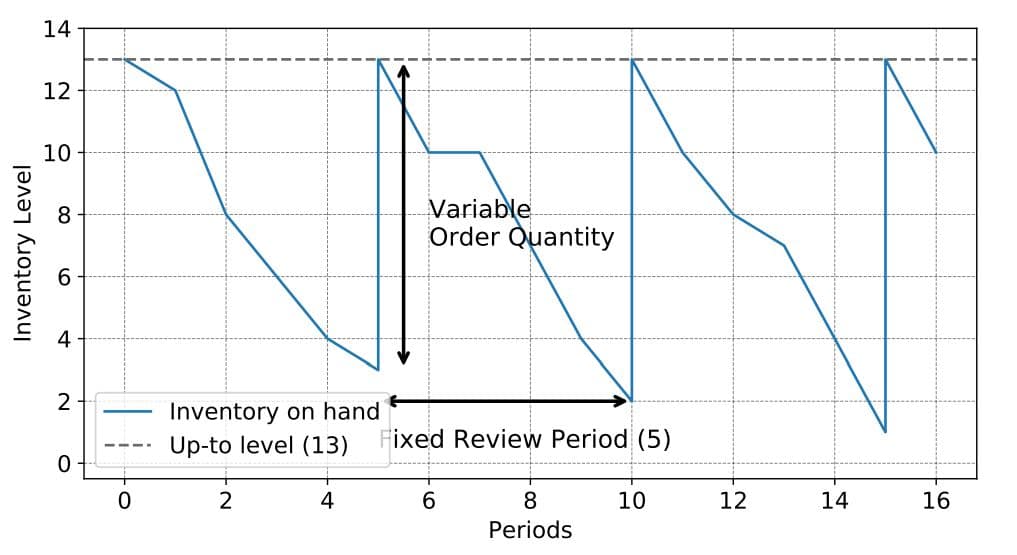
Benefits: The periodic replenishment is the most commonly used policy, because it allows you to group orders with the same supplier. This method benefits both your organization and your supplier by limiting exchanges, and by optimizing planning operations such as limiting the number of deliveries, and the loading of trucks or other means of transportation.
Limitations: A future article dedicated to safety stock, will demonstrate that this policy is, in fact, riskier than the order point policy because of activity problems that can arise from depletion. Indeed. if you are already out of stock on Monday and you can only place your order on Friday, you will be 4 days without stock, since it is impossible to order between two periods. This is likely to result in lost revenue and missed sales opportunities. This kind of problem does not exist with the order point (fixed replenishment) method.
Other inventory policies are possible
Many other inventory policies can be envisaged. Thus it is possible to replenish a fixed quantity, during each period. It suffices to set the trigger for a minimum order threshold. These differing policies can be adapted according to the needs of each activity. However, the formulas for calculating safety stock would then be much more complicated to implement.
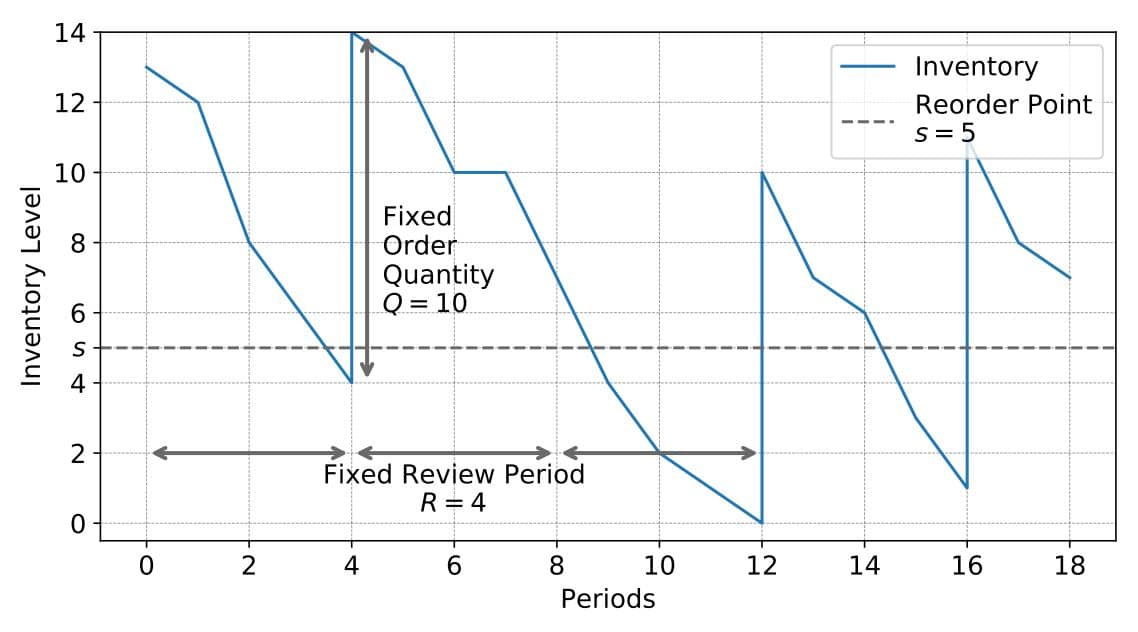
You can get more details on the different inventory management policies and demand forecasting methods in the book Data Science for Supply Chain Forecast, written by Nicolas Vandeput.
